Compressed Air?
Why is compressed air important?
Compressed air is an excellent medium for storing and transmitting energy, making it essential to the manufacturing sector and most industries. Compared to other energy storage methods such as batteries and steam, it is versatile and relatively safe to use. Unlike electricity, where overloading equipment may result in safety hazards such as electrical shocks and potential fires – it is a much safer alternative.
Compressed air powers today's modern society; from transportation via ships, trains and cars, to the mechanics of brake systems, suspensions and airbags, and utilising power tools from construction sites, dentist’s practices and in manufacturing. Today, it is considered the Fourth Utility amongst electricity, water and gas.
What is air quality?
As defined by the industry standard ISO 8573-1 for air purity, air quality is determined by the amount of water, solid particles and oil aerosols present, as according to the different quality classes of compressed air. This is a useful indicator of the amount of potentially harmful particles present.
Why consider the air quality and purity?
Ambient air contains a certain amount of moisture, dust particles and oil aerosols. These are mainly contributed by human and industrial activities. The amount and ratio of these contaminants depend on the season, ambient temperature and environment of the compressor’s location.
Since compressed air is generated on-site with compressors, when the air enters the compressor’s inlet and is compressed to 8 bar pressure, the concentration of undesirable particles increases by eightfold. These particles are so small that most of them pass through the compressor’s intake filter and enter the process line.
Without specialised purification processes, untreated compressed air may contain impurities such as solid particles (dirt, sand, soot, metal oxides, salt crystals, rust and pipe scale), liquid and oil aerosols, oil vapours and microorganisms (visible and invisible). The untreated compressed air forms a condensate mixture which can pose harmful risks to your industrial machinery.
Additionally, because of the heat of compression effect, the rise in temperature increases the its capacity to retain moisture. Exposure to excess moisture will deteriorate your pneumatic piping system and other machineries – impairing production results and increasing operational costs.
Facility managers must take steps to ensure the quality of the compressed air meets the required Class to avoid substandard product quality, unplanned downtime, loss of production, costly air leaks, equipment damage, and potential health and safety risks. Depending on application, untreated compressed air, can either lead to expensive downtime or adversely affect the quality of your end products.
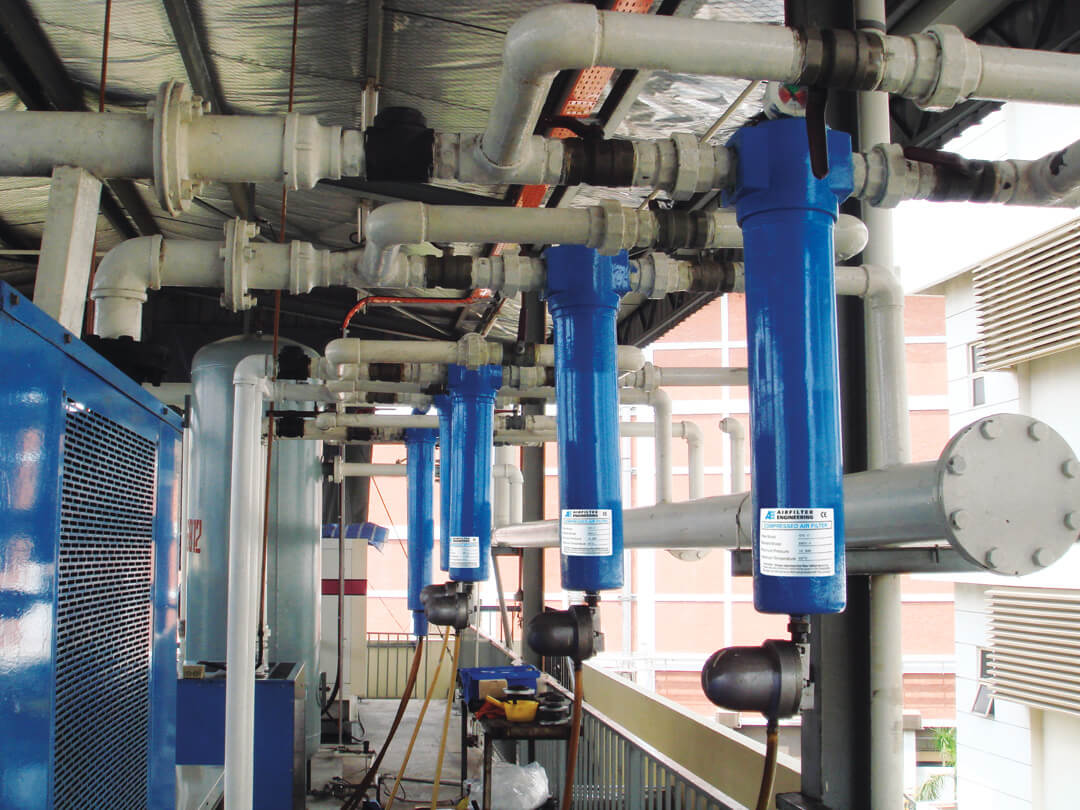
How does optimising your compressed air network help save cost?
Together with AFE, you can minimise production downtime and avoid potentially expensive accidents.
Incorporating our assortment of high-performance purification products optimises your compressed air network to run efficiently and reliably. Since compressors alone in the industrial sector utilise a large portion of all the energy consumed - through lowering your energy consumption, long-term energy and cost savings can be realised. At the same time, reducing your carbon footprint to meet your sustainability goals.
Regardless of the type of compressor installed, routine inspections and regular maintenance of the downstream treatment components such as filtration and adsorption systems should be complied with to keep energy costs down, avoid premature wear of tools and eliminate problems downstream.
As compressed air treatment specialists with over 30 years of experience, we recommend our customers to stick to the rule of thumb - invest in preventive maintenance, because it's worth it.
Prevention is better than cure,
or in this case -
cheaper, and much safer.
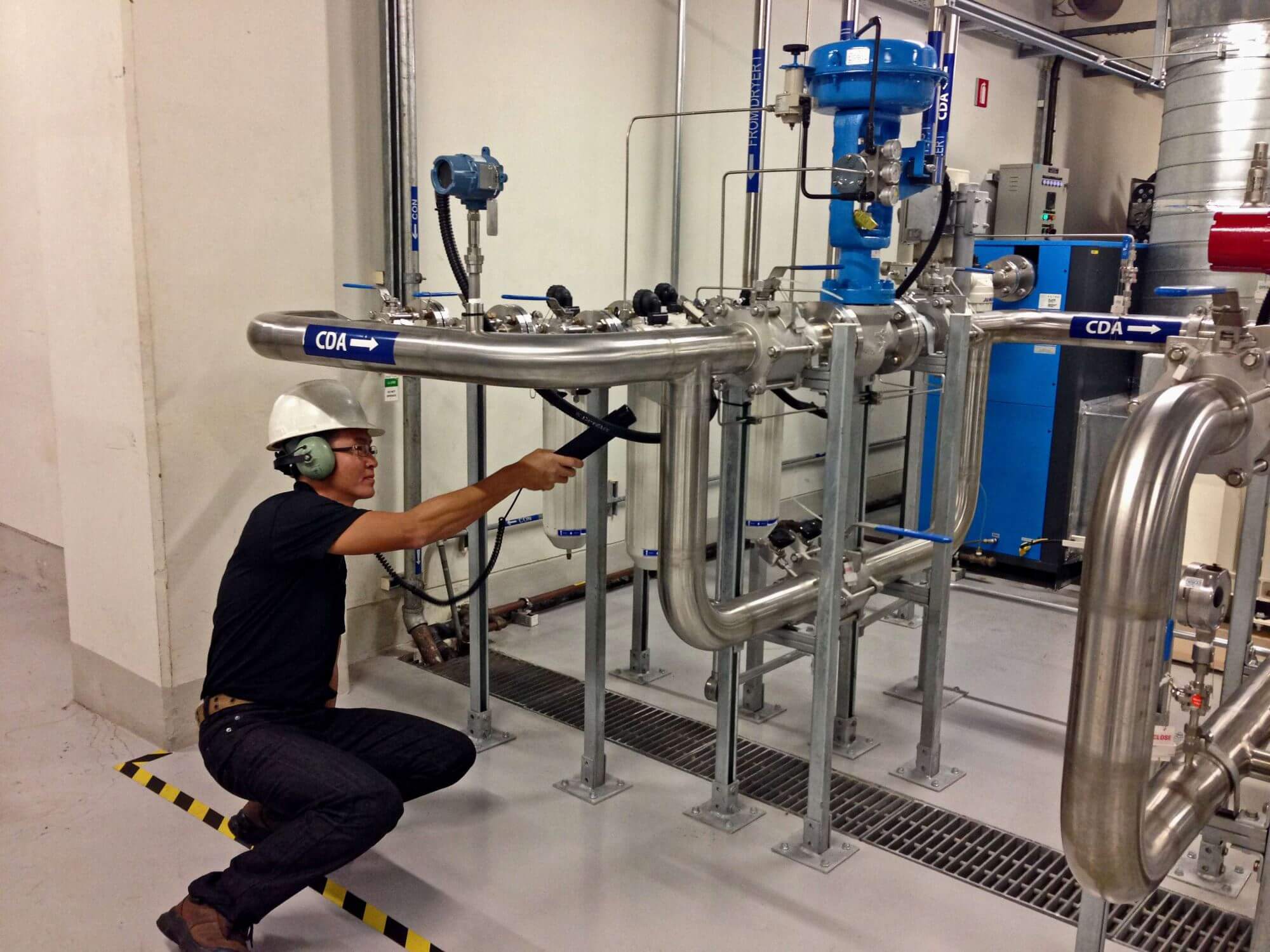
A Comprehensive Approach to Compressed Air Treatment
The basic principle of maintaining compressed air quality is that it should be treated twice; once prior to entering the compressed air distribution system and once more at each point of use.
In most cases, a single compressed air network supplies air to multiple applications under the same roof. Hence this two-pronged system design approach allows for the most cost-effective filtration solutions. It removes the residual contamination in the distribution system, while ensuring that the most critical processes use only the purest air.
Continue reading to find out how our products are key to this purification process.
Why do we need compressed air filters?
Compressed air filter are needed to separate contaminants from the compressed air stream. At AFE, we have developed a comprehensive range of filter grades to cater to the requirements of different applications. Available in a variety of sizes and series, our specialised pleated design ensures a higher filtration surface for the best performance.
After prolonged use, contaminants tend to build up on the filter media. This reduces the amount of available flow paths and increases the resistance in the flow path. This results in a pressure drop which indicates energy loss from the compressed air system. All filtering processes eventually lead to pressure drop. Finer filters that have tighter structure, cause a higher pressure drop and get clogged more quickly - demanding frequent filter replacement.
Our AFE filters are specially designed for low pressure drop. They are dimensioned to handle nominal flow properly, whilst having a larger capacity threshold to manage some pressure drop due to a certain amount of blockage. Engineered for the best performance, our AFE filters use high quality components designed for lowest pressure losses to maximise your energy savings whilst maintaining equipment performance.
Since pressure is an indicator of available energy, one should reduce pressure drop as much as possible by using correctly sized filters and replacing them regularly. Interested in optimising your current air filters? AFE offers compatible replacement elements for any filter – if we don’t have it, we can make it.
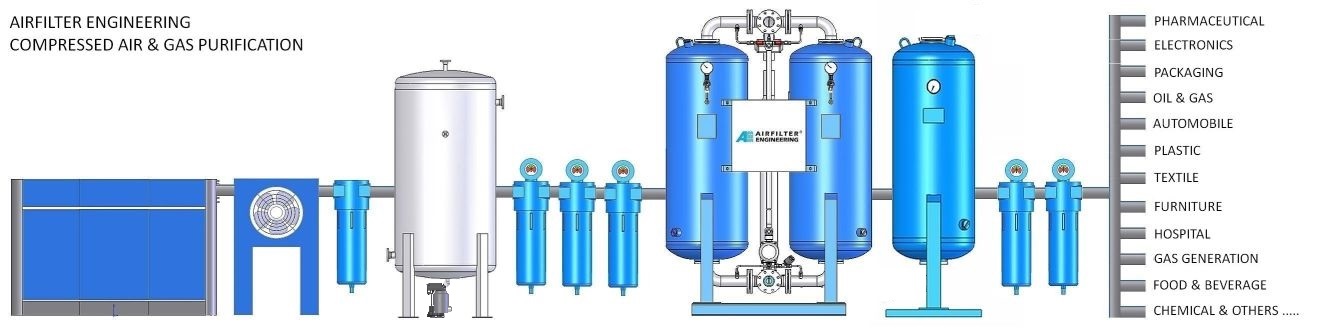
What Does Differential Pressure Tell Us?
Differential Pressure is the difference in pressure between two points in a fluid system, measured by the resistance to flow across the compressed air network. It describes the loss of energy available in a liquid or gas system – making it the metric that is directly correlated to energy savings.
All gases and liquids have mass and viscosity. This means that the relative motion between the fluid and surface of inner piping results in some frictional pressure. Likewise, any directional change in flow path results in a corresponding differential pressure. Energy is typically lost through resistance, as the compressed air travels through piping, ports and orifices, resistance against the filter media and resistance of contaminants collecting on the filter media.
Changes in the differential pressure are an indication of physical changes in the filters. A sudden drop in differential pressure drop may indicate a filter leak or rupture. As contaminants build on the filter, pressure drop across the filter increases. Filters reaching terminal pressure drops should be serviced or replaced accordingly.
All our AFE Filter Series have the option for a Differential Pressure Gauge to show pressure drop. The true purpose of a differential pressure monitoring device is to indicate premature blockage of a filter element, and should not be used as a filter service indicator.
How about removing condensate?
To prevent damage to your compressed air system, moisture should be removed as quickly as possible. AFE’s water separator are specially designed based on the proven centrifugal separation to remove up to 99% of water aerosols. Working in conjunction with other compressed air treatment products like filters, after-coolers and dryers, the water separator is a cost-effective addition to ensure that bulk water in the compressed air system is properly separated and discharged.
We offer a range of water separators as well as components to help you maintain a dry pneumatic system. The proven centrifugal mechanism of our water separator is simple, efficient and maintenance free.
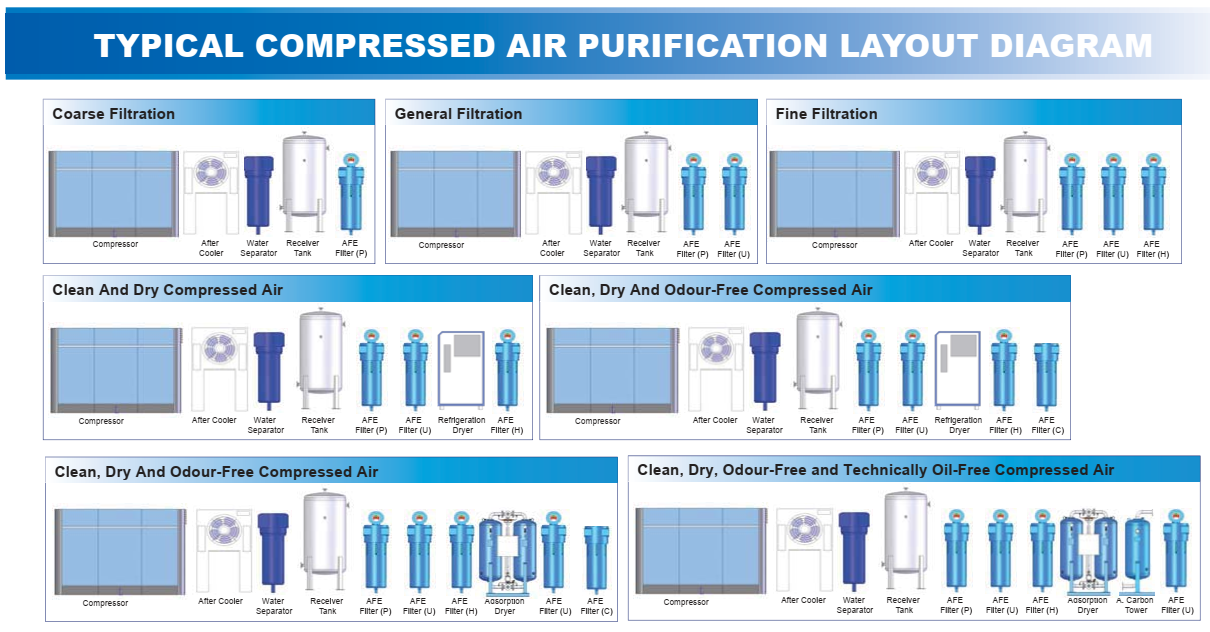
How do AFE Desiccant Dryers help?
Our highly efficient compressed air filters and condensate drains successfully remove most of the impurities. But depending on your application, this may not be enough. To achieve an even higher level of compressed air quality, dryers are essential to further removing moisture from the compressed air system. Condensing dryers are used when the maximum air quality required is Class 4, meaning the dew point is less than 3°C. If compressed air with even less moisture is required, meaning a lower pressure dew point, then an adsorption dryer must be installed.
Desiccant dryers are ideal for critical applications where very dry air is required, as a pressure dew point up to –70°C can be achieved. AFE designs and manufactures both heated and heatless desiccant dryers.
Desiccant dryers are installed downstream from the aftercooler and/or the refrigeration dryer. As compressed air passes through the dryer vessel, water vapour is absorbed by the desiccant material contained within.
Adsorption dryers are built with two drying vessels to regularly regenerate the desiccant so it can revitalise its drying capacity. Whilst first tower is drying the incoming compressed air, the desiccant in the second tower is being regenerated. The towers switch tasks once the other tower is completely regenerated.
To avoid large investments into a centralised purification system, our AFE series of compact desiccant dryers (C-HDD-N) can be incorporated at specific stages where higher quality air is needed in the production process. Our dryers utilise reliable adsorption technology; they offer uninterrupted drying capacity, provide security to your production operations and provide you pure and dry air when and where you need it.
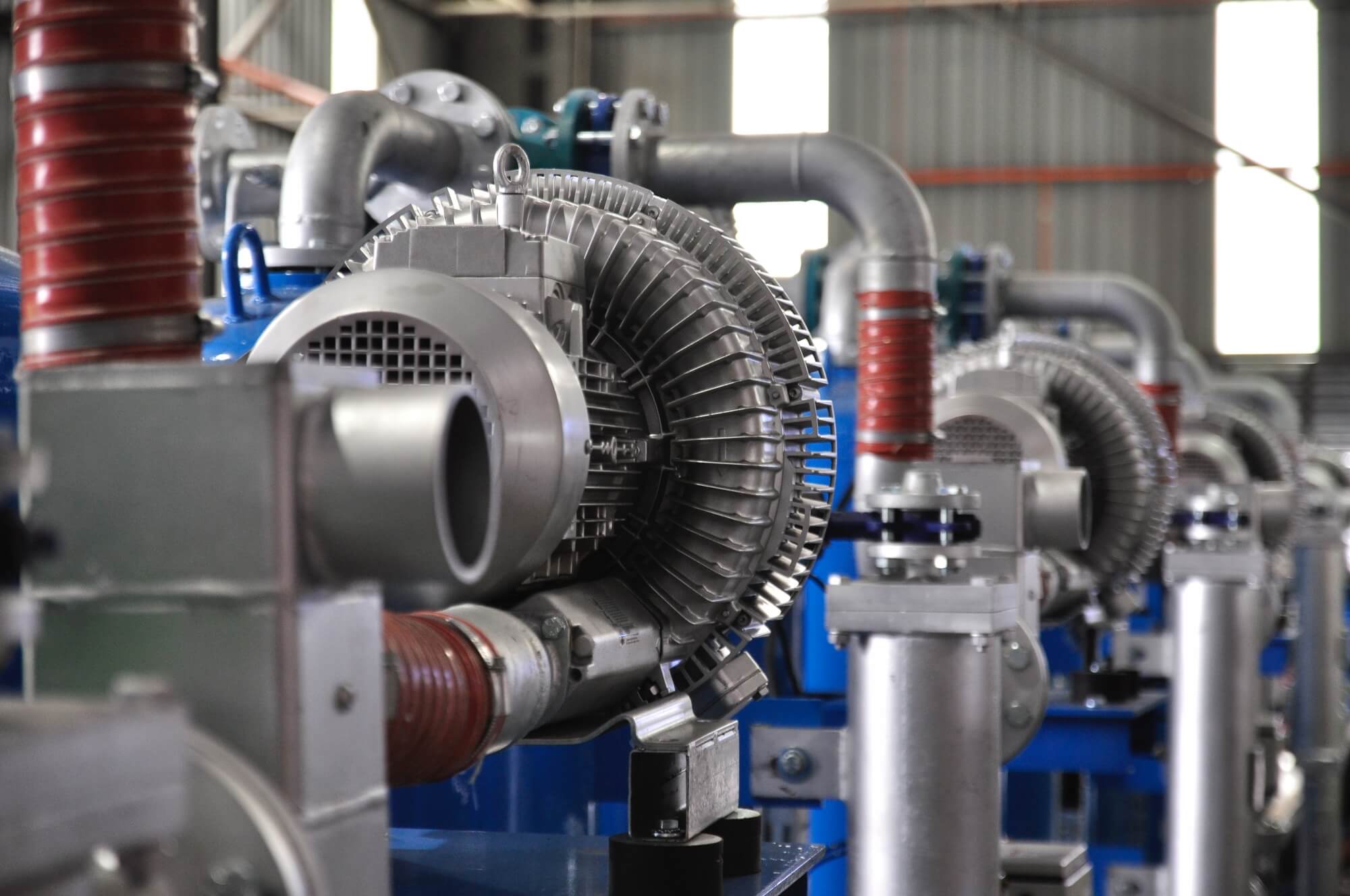
As compressed air continues gaining popularity as the 4th Utility, pneumatic powered technologies have also advanced rapidly. In turn, the demand for high-quality compressed air, free of undesirable substances, increases.
At AFE, we produce a wide range of products to meet this growing demand for clean, dry and oil-free air. Our team offer full-suite support to help you design a well-engineered filtration system that strikes a balance between high-efficiency, high capacity and a low differential pressure. Relying on us to provide your compressed air filtration needs, means that you’ll be working closely with a manufacturer that understands both your processing requirements and the drying and filtering products appropriate to address them.
Building on 30 years of experience, we make sure your equipment is well-sized with appropriate dew points and flow to preserve your assets, avoid downtime, and eliminate headaches down the line.
Looking for efficient and effective solutions?
Click that red button, and let's talk.